CNC boring mills are essential for producing precise and complex parts with demanding tolerances. At Weish, a leading CNC machine manufacturer, we recognize that achieving high-quality outputs from CNC boring mills requires not only precise machining but also the right finishing methods. This article explores various finishing techniques to enhance surface quality, durability, and performance of parts produced by CNC boring mills.
Importance of Finishing in CNC Boring Mills
Why Finishing is Crucial
Finishing is a critical step in CNC boring mill operations as it enhances surface quality, improves dimensional accuracy, and ensures that parts meet the specific requirements of their intended applications. A well-finished part is often more durable, resistant to wear, and aesthetically appealing.
Common Applications of CNC Boring Mill Finishing
From aerospace to automotive and heavy machinery manufacturing, industries rely on finished parts produced by CNC boring mills. Proper finishing not only ensures the part’s performance but also increases its lifespan, making it suitable for high-stress and precision applications.
Common Finishing Methods for CNC Boring Mills Outputs
1. Surface Grinding
Surface grinding is a precise finishing method that removes minimal material from the part surface, creating a smooth, high-quality finish. This technique is especially useful for flat and parallel surfaces, ensuring tight tolerances and dimensional accuracy.
Benefits of Surface Grinding
- Enhanced Surface Smoothness: Creates a polished, smooth surface that improves functionality and aesthetics.
- Improved Dimensional Accuracy: Ideal for parts that require strict tolerances.
- Reduced Friction: A smoother surface reduces friction, essential in parts used in high-stress applications.
At Weish, we employ surface grinding to provide a superior finish for parts that need an ultra-smooth surface and precise dimensions.
2. Honing
Honing is a finishing process that uses abrasive stones or sticks to remove fine layers of material from the inner surfaces of bored holes. This technique is commonly used for cylindrical surfaces and ensures high precision and superior finish.
Advantages of Honing
- Improved Hole Quality: Honing creates precise hole diameters and improves roundness.
- Enhanced Surface Finish: Offers a smooth finish with a high level of control over the material removal process.
- Consistency in Production: Ensures uniformity across multiple parts, essential in high-volume production.
Weish’s CNC boring mills are compatible with honing, allowing us to deliver components that meet exacting standards, especially for applications that require tight tolerance control.
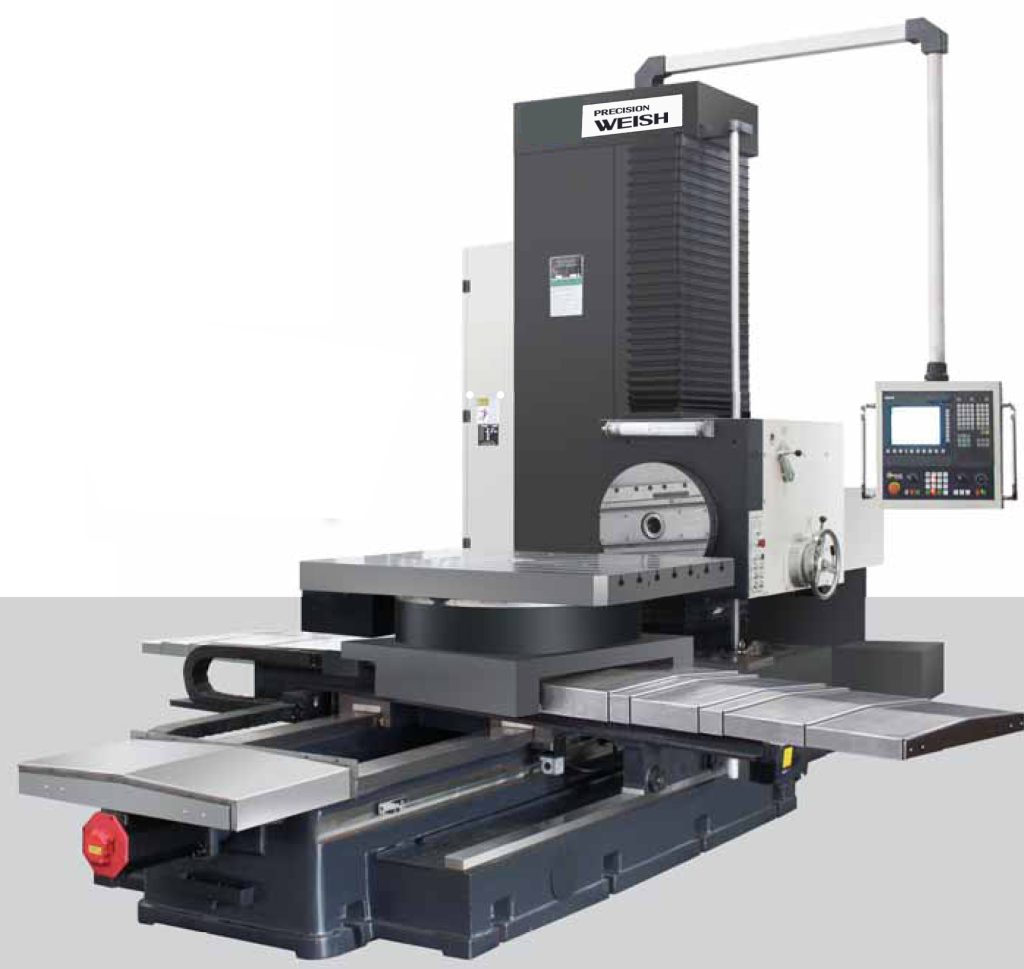
3. Lapping
Lapping is a process that uses a loose abrasive between two surfaces to remove very small amounts of material. It produces an extremely smooth, flat, and uniform surface and is often used for parts that demand the highest levels of surface finish and dimensional accuracy.
Benefits of Lapping
- Ultra-Smooth Finish: Ideal for parts requiring high surface finish, such as optical components.
- High Dimensional Accuracy: Provides precision measurements in parts used in precision equipment.
- Wear Resistance: Enhances durability, especially important in moving parts.
At Weish, we use lapping for parts that require mirror-like finishes and extremely tight tolerances, catering to high-end applications across industries.
4. Burnishing
Burnishing is a finishing technique that involves pressing a hardened tool onto the surface of the part, smoothing out irregularities through plastic deformation. This method improves surface hardness and creates a shiny, polished finish.
Benefits of Burnishing
- Increased Surface Hardness: Burnishing improves the hardness and wear resistance of the part.
- Enhanced Finish Quality: Produces a polished, shiny surface ideal for parts that need a cosmetic finish.
- Improved Fatigue Resistance: Reduces the risk of micro-cracks, enhancing part longevity.
Weish recommends burnishing for parts that require both a high-quality finish and additional durability, such as components exposed to repetitive stress.
5. Polishing
Polishing is a finishing method that uses abrasive materials to remove surface imperfections and create a high-quality, shiny finish. Polishing can be done manually or with automated equipment, depending on the part’s size and complexity.
Advantages of Polishing
- Enhanced Aesthetics: Ideal for parts with visible surfaces, such as decorative components.
- Reduced Friction: A polished surface reduces friction in moving parts, improving efficiency.
- Corrosion Resistance: Removes surface impurities, helping to prevent corrosion.
At Weish, we use polishing on parts that require both aesthetic appeal and functional performance, ensuring each component is ready for end-use in demanding applications.
6. Chemical and Electrochemical Machining (ECM)
Chemical and electrochemical machining are non-traditional finishing methods that remove material without mechanical force. In ECM, an electrolyte is used to dissolve surface imperfections, achieving precise results without affecting the material’s structural integrity.
Benefits of ECM in CNC Finishing
- No Heat or Mechanical Stress: Prevents material deformation, ideal for delicate or complex parts.
- High Precision: Provides a smooth, high-quality surface with fine detail.
- Reduced Tool Wear: As no physical contact is involved, ECM reduces tool wear and maintenance.
Weish employs ECM in scenarios that demand high precision and minimal impact on material properties, particularly for parts used in precision and sensitive environments.
Advanced Finishing Techniques for Enhanced Durability
1. Hard Coating
Hard coating applies a thin layer of hard material, such as titanium nitride (TiN) or diamond-like carbon (DLC), to the surface of the part, significantly increasing its wear and corrosion resistance.
Benefits of Hard Coating
- Enhanced Durability: Ideal for parts exposed to high wear and corrosive environments.
- Improved Performance: Reduces friction, improving part efficiency.
- Extended Part Life: Hard coating protects the underlying material, extending part longevity.
At Weish, we offer hard coating solutions for parts that need extra protection, especially for components used in heavy-duty applications.
2. Anodizing
Anodizing is an electrochemical process that forms a durable, corrosion-resistant oxide layer on the surface of metal parts, commonly used for aluminum and its alloys.
Advantages of Anodizing
- Corrosion Resistance: Provides excellent protection against corrosion.
- Improved Aesthetic Options: Anodized surfaces can be colored for customization.
- Durability: Increases the surface hardness of the part.
Weish uses anodizing for aluminum components, particularly for parts that require both corrosion resistance and an appealing finish.
3. Plating (Chrome, Nickel, etc.)
Plating involves applying a thin layer of metal, such as chrome or nickel, to the surface of the part to improve its corrosion resistance, hardness, and appearance.
Benefits of Plating
- Corrosion Protection: Prevents oxidation, especially in corrosive environments.
- Enhanced Aesthetics: Provides a shiny, attractive finish.
- Increased Wear Resistance: Adds a hard layer, protecting the part from scratches and wear.
Weish recommends plating for components that require additional durability and a polished look, particularly in applications involving frequent handling or exposure to moisture.
How Weish Ensures High-Quality Finishing for CNC Boring Mills Outputs
1. Precision Control Systems
At Weish, our CNC boring mills are equipped with advanced control systems that allow for precise adjustments in machining and finishing processes. This ensures that each part meets the exact specifications and quality standards.
2. Skilled Technicians and Quality Inspections
Our team of skilled technicians performs thorough quality inspections after each finishing stage. This ensures that every component leaving our facility meets the stringent requirements of our customers.
3. Customized Finishing Solutions
Weish understands that each project is unique, so we offer customized finishing options based on material, application, and client requirements. This flexibility enables us to deliver optimal results for a wide range of industries.
Conclusion: Trust Weish for High-Quality CNC Boring Mills Outputs
For high-quality results from CNC boring mills, precise finishing is essential. At Weish, we employ a variety of finishing methods, from surface grinding and honing to advanced techniques like ECM and hard coating, to ensure each part meets industry standards for performance, durability, and aesthetics.
With our commitment to quality, advanced equipment, and skilled team, Weish is the go-to CNC machine manufacturer for businesses that demand excellence. For high-quality, expertly finished CNC boring mill outputs, contact Weish today to discover how our finishing solutions can meet your project needs.